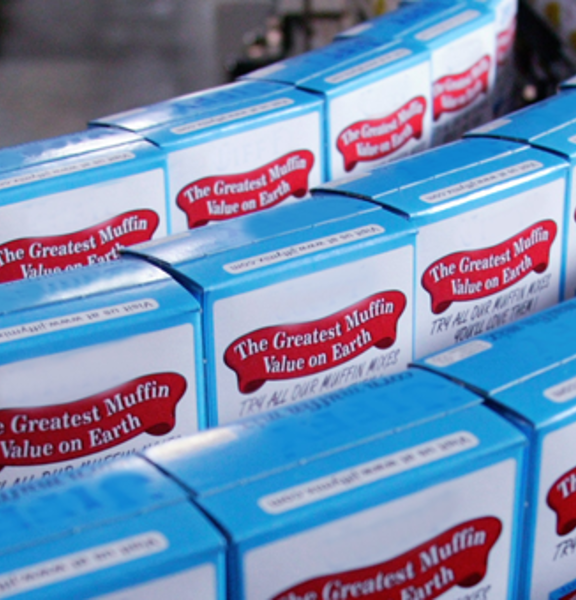
Automation – how will greater adoption benefit UK PLC?
Date: Wednesday 6 March
Location: Streamed from the Manufacturing Technology Centre, Ansty Park Coventry
This inaugural event aimed to set the scene of where UK PLC is now, compared to its global competitors, and why and how it needs to change to advance our country’s manufacturing sector. Barriers to adoption were explored, common myths around automation were busted and a real-life experience of automation from an SME was shared.
Our Panellists
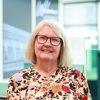
Gail Hunt
Facilitator and hostGail has been writing about manufacturing technologies across several trade publications for over 30 years. She has worked as a business-to-business journalist with such titles as Food Manufacture, Fine Food Digest, Artisan magazine, The Grocer, British Baker, Builders Merchants Journal and DIY Week. While editor of Packaging News she won several awards and for the last 13 years she has been editor of Machinery Update, the machinery-only journal published by Automate UK. She stepped down from the magazine at the end of 2023 to work on projects for Automate UK including this new UK Automation Forum.
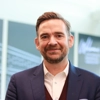
Peter Williamson
CEO, Automate UK (formerly the PPMA Group)In his role as CEO of leading trade body Automate UK, Peter is looking to use his 25 years of experience in robotics and automation to support end users in adopting the latest in automation technology and to help raise awareness of the benefits that automation can bring to UK manufacturing. His experience comes from RARUK Automation, a company he formed in 2016 that is now a world leading supplier of collaborative robots (or cobots), and for which he is also now a non-executive director.
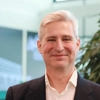
James Selka
CEO, Manufacturing Technologies Association (MTA)James has accumulated over 25 years of manufacturing experience, including 13 years as Managing Director of a specialist high precision, internationally trading, supplier of turnkey instrument sub-systems and prior to joining the MTA, he was Production and HR Director at a major manufacturer of mechanical seals and support systems. James brings knowledge about global manufacturing, a strong interest in supply chains together with logistics, and is an expert on global advanced manufacturing. He regularly participates in policy formation in the UK, Europe and further afield.

Oliver Selby
Head of Sales at specialist automation company FANUC UKWith 20 years of experience in factory automation, Oliver brings a wealth of industry and product knowledge of UK manufacturing and engineering to the Forum. He is passionate about strategically transforming the UK’s automation and manufacturing position on the global stage which can be seen through his customer first philosophy and drive to improve manufacturing businesses efficiency and profitability using modern technology.
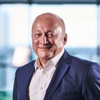
Mike Wilson
Chair UK Automation Forum & Chief Automation Officer, Manufacturing Technology Centre (MTC)Mike has over 40 years of experience in the application of automation to manufacturing across a broad range of industry sectors and is widely recognised as one of the leading authorities on the application of industrial robot systems in the UK. At the MTC, he is leading the drive to increase the adoption of robotics and automation in the UK. He is also a Director of the Manufacturing Technologies Association, Council member and past Chairman of the British Automation and Robot Association and has previously been Chairman of the International Federation of Robotics.
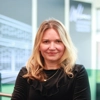
Nina Gryf
Senior Policy Manager, MAKE UKNina works closely on Make UK’s Delivering Unlocking Innovation campaign, which strongly focuses on the role of innovation and technology in increasing productivity and competitiveness. Her role cuts across all of Make UK’s core campaigns. She is the lead author of Make UK’s Innovation Monitor which tracks manufacturers’ progress on digital adoption. She has spoken on the importance of accelerating digital adoption to manufacturers and policymakers alike and has spoken publicly on the need for the Government to ensure the industry has access to skills and finance to take full advantage of Industrial Digital Technologies.
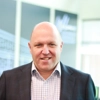
Jonathan Thacker
Operations Director, The Walsall Wheelbarrow Company LimitedJonathan is one of the founding directors of the Walsall Wheelbarrow Company, a family-owned business in which he has played a major role in the implementation and development of automation. He has worked with automation companies and financial institutions to secure investment for the initial installation phase and is the main decision maker/strategist for future development which includes a bespoke final assembly cell in 2025. The company is the only manufacturer of wheelbarrows in the UK and today, has the capacity to manufacture over 500,000 wheelbarrows a year. The Thacker family has been involved in wheelbarrow manufacturing since the 1940s and continues to invest in current and emerging technologies.
Watch the full webinar below
Learnings from this event
This event tackled the issue of poor robot take up in the UK , why this was, and how it could be overcome going forward.
Currently, the UK comes 25th in the international league table of robot density (number of robots per 10,000 employees in manufacturing) and faced with these global figures, the Forum panel set out the reasons why it is so crucial for UK PLC to adopt more robotic systems in their factories. Productivity gains are number one; helping to achieve net zero ambitions is another, addressing labour shortages is also important as well as delivering our sovereign manufacturing goals.
The panel felt that politicians, of whatever persuasion, needed to better understand the current manufacturing issues and that a change of strategy for the UK was necessary. Indeed, what would really help would be a coherent industrial strategy with a clear vision as to what was needed across industry and in education across all levels. Meanwhile, a highlight of the event was an SME company sharing its road to adopting robotics, how this had worked, how to avoid pitfalls, and the benefits it has enjoyed since their deployment.
Download hereList of audience Q&As below
Would the employer be responsible for re-training to use automation
(Peter Williamson) Whilst the employer would likely be responsible for the cost of providing the training, the majority of providers of robotics and automation have dedicated personnel and resources to train the end users.
(Oliver Selby) As a supplier of equipment and turn key equipment we provide training on the individual pieces of equipment as well as the whole production cell. This then feeds into the customers buyoff and PUWER assessment.
When you made the decision to automate, what did your process entail to gain the knowledge and then actually deploy? Because I believe lots of businesses understand the benefits of automation, but really don’t know where to start. They feel they need to do everything at once and it can be overwhelming.
(Mike Wilson) We understand the challenge of starting. The key is to find the right application with which to start. This might not be the biggest issue in the factory. It should often be a relatively simple application because there is a learning curve as with all things. Start with something simpler and lower risk and move on to the more complex applications later. There are independent sources of advice who can help with identifying the best place to start and the best suppliers to work with.
Can automated machinery run overnight unsupervised from a Health & Saftey propective
(Oliver Selby) In some cases yes, but very much dependent on the process that is being conducted, and the risks that are identified and how they can are proactively or reactively mitigated. (For example an automated welding line is generally manned through risk of fire, but with the right safety in place could run unsupervised)
I think the focus on robots scares off some SMEs who assume Automation is only for large manufacturers who think 'It's not for me!'. Lower scale automation using cartesian robots or electrical actuators is a lower-cost, entry level way to begin the automation journey. It's hard to jump straight in with a big orange robot.
(Mike Wilson) I agree that buying a large, complex, expensive is not the right first step. It is about buying the appropriate automation which might be a simple actuator or a robot. Getting started is key. By the way robots are not as expensive as many people think.
Its important to walk before you run especially with SME's Cobot's can be a good route work with the senior team as well as the team responsible show all depts the benefits..
(Peter Williamson) Completely agree with this statement. Cobot technology can be adopted in a fairly straightforward way for simple tasks. It is key to gain confidence in automation throughout the business and using technology that is potentially more attainable to take on tasks that are reasonably easy to automate is a great way to get started.
Agree companies need hands held through automation explain productivity efficiency benefits..
(Mike Wilson) Agreed. Advice does help to reduce risks and can help to build a stronger case to justify investment.
Trust and integrity are key to discussions
(Mike Wilson) Agreed. Picking the right supplier, building long term relationships are important. Don't buy the lowest cost just because it is the cheapest.
Can BARA help manufacturers start on their automation jouney?
(Peter Williamson) Absolutely. BARA can support manufacturers in a number of ways in starting on their automation journey. There are a number of resources on the BARA website that provide practical advice on where and how to start. If a manufacturer needs more specific guidance, then they should reach out to BARA through the Automate UK website so that our team can provide support and point the company in the right direction of one of our members who would be able to provide the right solutions for their production challenges.